I. Introduction
A. Definition of Permanent Magnet Generators
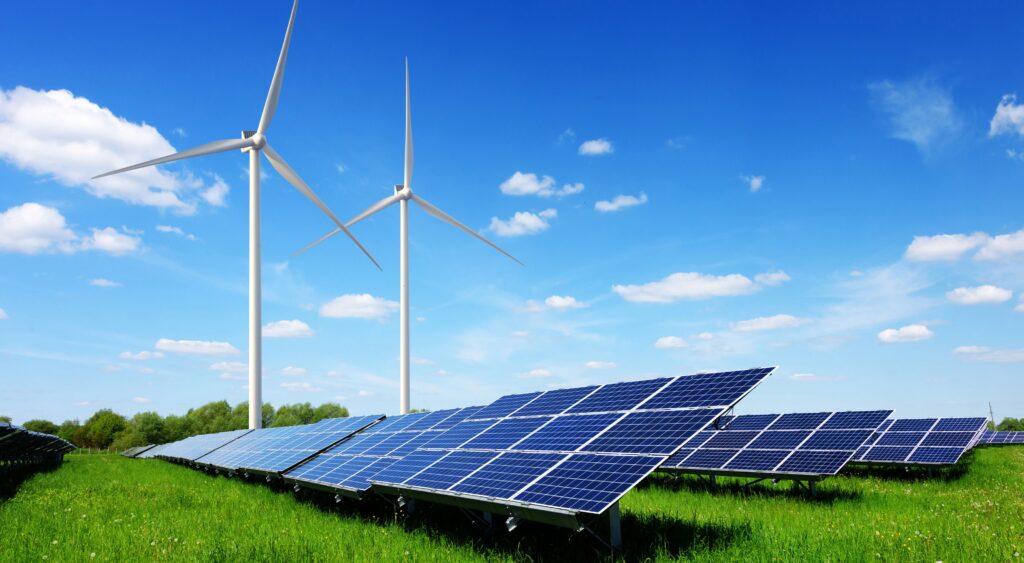
Permanent magnet generators are devices that convert mechanical energy into electrical energy by using permanent magnets to create a magnetic field in a stationary position. The rotation of a rotor within this magnetic field induces an electrical current in the stator coils, which is then converted into usable electrical power. These generators are commonly used in applications where a reliable and efficient source of electricity is required, such as in wind turbines, hydroelectric power plants, and portable power systems. They are known for their low maintenance requirements and long lifespan, making them a popular choice for renewable energy systems.
B. Importance of Renewable Energy Systems
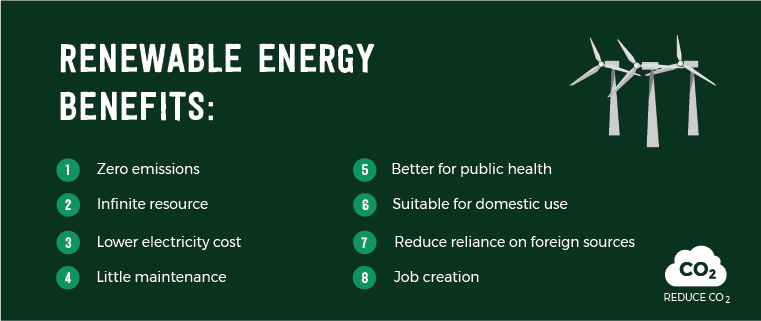
Renewable energy systems are becoming increasingly important due to several reasons, including:
1. Climate Change: The burning of fossil fuels has been identified as a major contributor to climate change, which is leading to more frequent and severe natural disasters, rising sea levels, and other negative impacts on the environment. Renewable energy systems, such as solar, wind, and hydropower, emit little to no greenhouse gases, making them a key solution to address climate change.
2. Energy Security: Renewable energy systems can provide a more secure source of energy compared to fossil fuels, which are subject to price volatility and geopolitical tensions. By diversifying the energy mix with renewable sources, countries can reduce their dependence on imported fossil fuels and increase their energy independence.
3. Economic Benefits: Renewable energy systems can provide economic benefits by creating jobs in the manufacturing, installation, and maintenance of renewable energy infrastructure. Additionally, renewable energy systems can help reduce energy costs for consumers and businesses over the long term.
4. Health Benefits: Fossil fuels are a major source of air pollution, which can lead to respiratory and cardiovascular diseases. Renewable energy systems, on the other hand, do not produce harmful emissions and can help improve air quality and public health.
Overall, renewable energy systems are crucial for a sustainable and resilient future, and their importance will continue to grow as we work towards a cleaner and more sustainable energy system.
C. Purpose of the Guide
The purpose of A Comprehensive Guide to Permanent Magnet Generators for Renewable Energy Systems is to provide a complete understanding of permanent magnet generators (PMGs) and their role in renewable energy systems. The guide aims to educate readers on the principles behind PMGs, their advantages and disadvantages, and the different types of PMGs available. It also covers the design and construction of PMGs, as well as their maintenance and troubleshooting. The guide is intended to help individuals and organizations interested in renewable energy systems to make informed decisions about the use of PMGs in their projects.
II. Types of Permanent Magnet Generators
A. Axial Flux Permanent Magnet Generators
Axial flux permanent magnet generators (AFPMGs) are a type of electric generator that uses permanent magnets to produce electrical energy. They are often used in wind turbines and other renewable energy applications where high efficiency and low maintenance are important.
AFPMGs are designed with a flat, disc-shaped rotor that rotates around a central axis. The rotor is mounted with permanent magnets that are arranged in a radial pattern. The stator, which is stationary, is made up of a series of coils that are positioned around the rotor.
When the rotor rotates, the magnets pass by the coils in the stator, generating an electrical current. The design of the AFPMG allows for a high power density, meaning that a large amount of power can be generated in a small space.
One advantage of AFPMGs is that they are highly efficient, with conversion rates of up to 90%. They also have a low maintenance requirement, as there are no brushes or slip rings to wear out.
AFPMGs are becoming increasingly popular in renewable energy applications, particularly in small-scale wind turbines for home and farm use. They are also used in some electric vehicles, such as bicycles and scooters.
B. Radial Flux Permanent Magnet Generators
Radial flux permanent magnet generators are a type of electric generator that uses permanent magnets to produce electrical power. In these generators, the magnetic field is oriented radially, perpendicular to the axis of rotation. This configuration allows for a compact design and high power density.
In a radial flux generator, the permanent magnets are mounted on the rotor, which rotates inside a stator containing the windings. As the rotor spins, the magnets induce an electrical current in the windings of the stator, which is then collected and used as electrical power.
Radial flux generators are commonly used in small-scale renewable energy systems, such as wind turbines and hydroelectric generators. They are also used in some automotive applications, such as hybrid and electric vehicles.
Advantages of radial flux permanent magnet generators include high efficiency, low maintenance requirements, and a compact design. They are also able to generate power at low speeds, making them well-suited for use in renewable energy systems that operate at variable speeds.
Overall, radial flux permanent magnet generators are a reliable and efficient way to produce electrical power, making them a popular choice for a variety of applications.
C. Comparison of Types
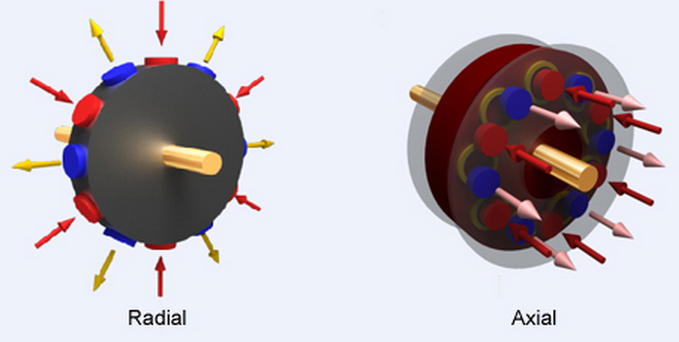
Radial Flux Permanent Magnet Generators (RFPMG) and Axial Flux Permanent Magnet Generators (AFPMG) are two types of permanent magnet generators that are widely used in various applications. Both RFPMG and AFPMG are designed to convert mechanical energy into electrical energy using permanent magnets. However, there are some significant differences between the two types of generators, which are discussed below:
1. Design: The design of RFPMG is such that the magnetic field is radial, which means it moves from the center of the generator to the outer edge. On the other hand, the design of AFPMG is such that the magnetic field is axial, which means it moves from the top of the generator to the bottom.
2. Efficiency: AFPMG is generally considered to be more efficient than RFPMG because it has a shorter air gap between the stator and rotor, which reduces the magnetic resistance and increases the power density. However, RFPMG can be designed to have a high efficiency by using optimized magnetic circuitry.
3. Size and Weight: RFPMG is generally larger and heavier than AFPMG because of the radial design, which requires a larger diameter to accommodate the magnets. AFPMG, on the other hand, has a compact design that allows it to be smaller and lighter.
4. Cost: RFPMG is generally less expensive than AFPMG because of the simpler design and manufacturing process. However, the cost difference depends on the specific application and the required performance.
5. Maintenance: AFPMG requires less maintenance than RFPMG because it has fewer moving parts and is less prone to wear and tear. RFPMG, on the other hand, requires periodic maintenance to ensure the optimal performance of the generator.
In conclusion, both RFPMG and AFPMG have their advantages and disadvantages, and the choice between the two depends on the specific application requirements, such as power output, efficiency, size, weight, and cost.
III. Design Considerations for Permanent Magnet Generators
A. Magnet Selection:
The choice of magnet material is critical for permanent magnet generators. The most commonly used magnets are neodymium-iron-boron (NdFeB) and samarium cobalt (SmCo). The magnets must have high magnetic flux density, high coercivity, and high maximum energy product. The selection of the magnet material should also consider the operating temperature, resistance to demagnetization, and cost.
B. Coil Design and Winding:
The coil design and winding are important factors in achieving high efficiency and power output. The coil should be designed to minimize losses due to resistance and eddy currents. The winding should be made of high-quality copper wire, and the number of turns should be optimized to achieve the desired voltage and current output.
C. Core Material Selection:
The core material is an important factor in determining the efficiency and power output of the generator. The core should be made of a material with high magnetic permeability, low hysteresis losses, and low eddy current losses. Commonly used core materials include laminated steel, iron powder, and amorphous metal.
D. Cooling System Design:
The cooling system is critical for maintaining the temperature of the generator within safe limits and preventing thermal damage to the magnets and coils. The cooling system should be designed to provide adequate heat transfer and cooling capacity, and it should be able to operate under varying ambient conditions.
E. Mechanical Design and Mounting:
The mechanical design and mounting of the generator should be optimized for the specific application. The generator should be designed to withstand the forces and vibrations associated with the application, and it should be mounted securely to prevent movement or damage.
F. Control and Protection System:
The control and protection system is essential for the safe and efficient operation of the generator. The system should include protection devices such as overcurrent and overvoltage protection, as well as a control system to regulate the output voltage and frequency. The control system should be designed to operate under varying load conditions and should be able to respond quickly to changes in the load.
IV. Applications of Permanent Magnet Generators in Renewable Energy Systems
A. Wind Turbine Generators:
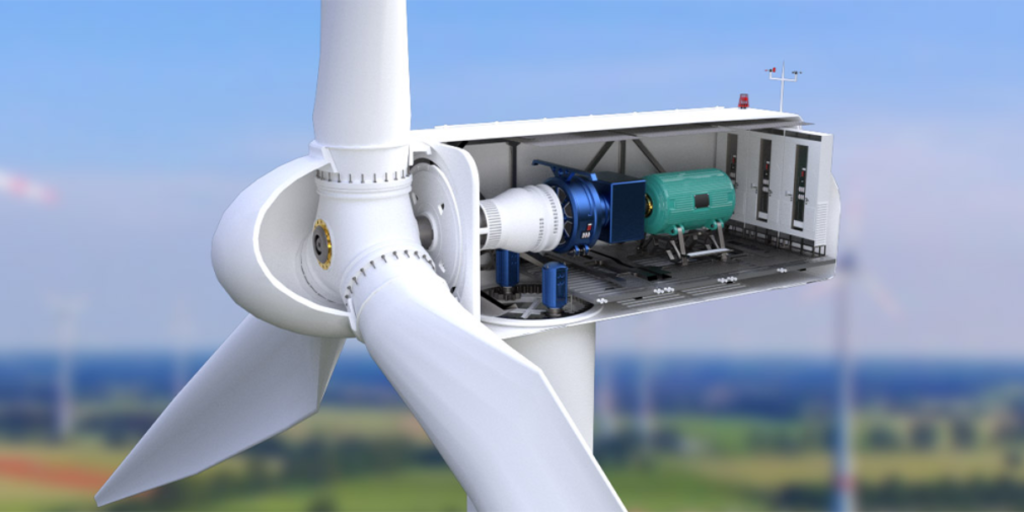
Permanent magnet generators (PMGs) are widely used in wind turbine generators. These generators are often found in small-scale wind turbines, which are used to generate electricity in remote locations or for home use. The PMG is a key component in these turbines, as it converts the rotational energy from the blades into electrical energy. The advantages of using a PMG in wind turbines include high efficiency, low maintenance, and long lifespan. Additionally, PMGs are lightweight and compact, which makes them a good fit for small-scale wind turbines.
B. Hydro Turbine Generators:
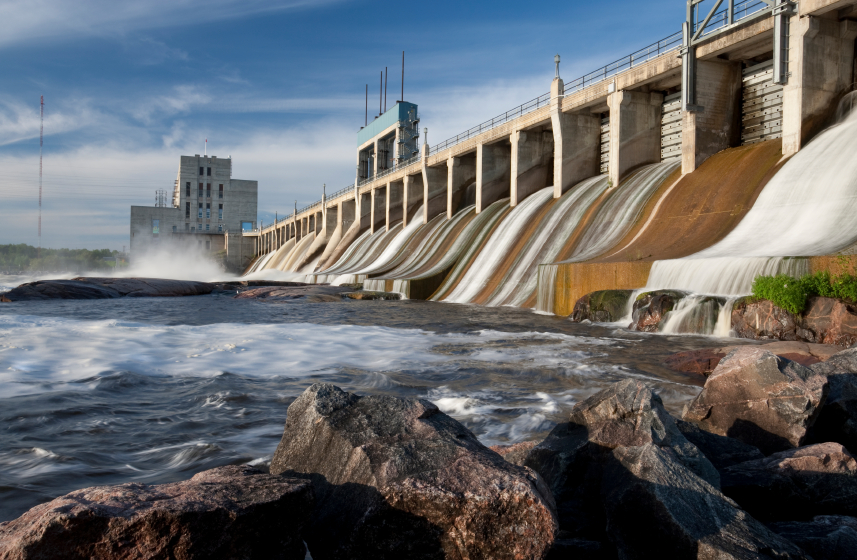
PMGs are also used in hydro turbine generators, which convert the energy from flowing water into electrical energy. These generators are commonly used in hydropower plants, where they produce large amounts of electricity. PMGs are preferred over other types of generators in hydro turbine systems because they are more efficient, have higher power density, and are more reliable. Additionally, PMGs are resistant to corrosion and require less maintenance than other types of generators.
C. Solar Power Systems:
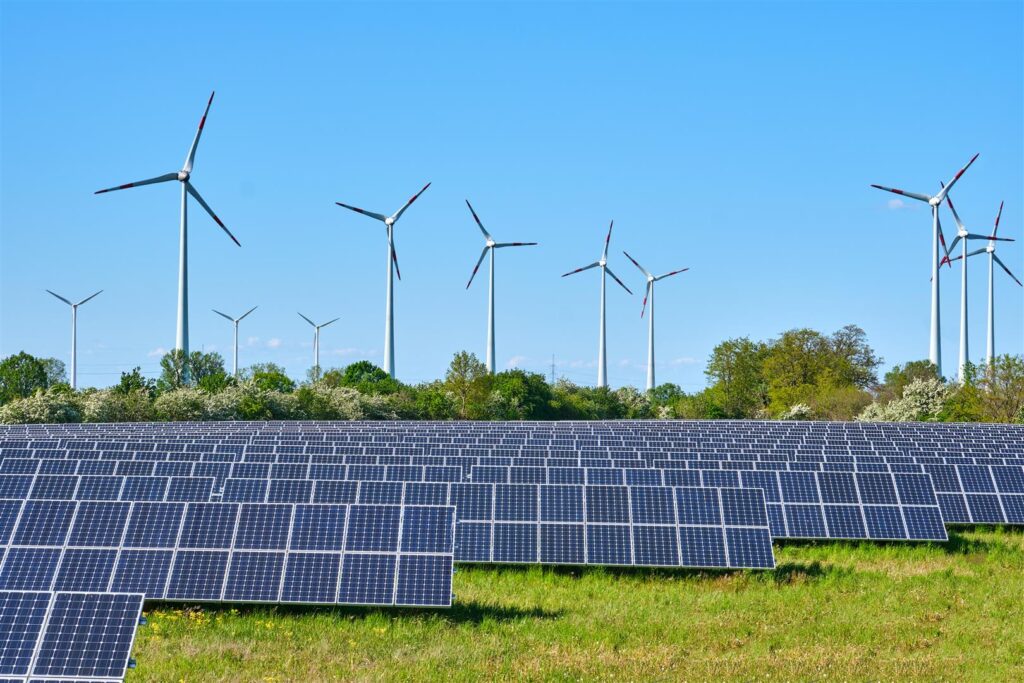
PMGs are used in solar power systems to convert the DC power produced by solar panels into AC power that can be used by homes and businesses. These generators are commonly found in off-grid solar systems, where they provide a reliable source of electricity. PMGs are preferred over other types of generators in solar power systems because they are more efficient, have a longer lifespan, and are more reliable. Additionally, PMGs are lightweight and compact, which makes them a good fit for small-scale solar systems.
V. Maintenance and Troubleshooting of Permanent Magnet Generators
A. Regular Maintenance Procedures
Permanent magnet generators are widely used in wind and hydropower systems due to their high efficiency and low maintenance requirements. However, like any other machine, they require periodic maintenance to ensure their optimal performance and longevity. Here are some regular maintenance procedures for permanent magnet generators:
1. Visual Inspection: A regular visual inspection of the generator is necessary to check for any signs of damage or wear. Look for any cracks, corrosion, or loose connections in the rotor, stator, and bearings. Check the alignment of the rotor and stator to ensure the smooth operation of the generator.
2. Lubrication: Proper lubrication of the bearings is essential for the smooth operation of the generator. Check the oil level and quality regularly, and replace it if necessary. Use the recommended lubricant and follow the manufacturer’s guidelines for lubrication intervals.
3. Cleaning: Keep the generator clean and free of dirt and debris. Use a soft brush or compressed air to remove any debris from the rotor and stator. Avoid using water or solvents for cleaning as they can damage the insulation.
4. Temperature Monitoring: Monitor the temperature of the generator regularly to ensure it stays within the recommended range. High temperatures can cause damage to the insulation and bearings, while low temperatures can cause condensation and corrosion.
5. Vibration Analysis: Regular vibration analysis can detect any abnormalities in the generator’s operation. This can help identify any potential problems early on and prevent costly repairs.
6. Electrical Testing: Test the electrical components of the generator regularly to ensure they are functioning correctly. Check the voltage, current, and resistance of the generator using a multimeter or other testing equipment.
By following these regular maintenance procedures, you can ensure the optimal performance and longevity of your permanent magnet generator. It is essential to follow the manufacturer’s guidelines for maintenance intervals and procedures to avoid any damage or premature failure of the generator.
B . Common Issues and Solutions
1. Overheating: This is a common issue with permanent magnet generators, especially when they are overloaded. The solution is to ensure proper ventilation and cooling mechanisms are in place.
2. Vibration: Excessive vibration can cause damage to the generator and its components. The solution is to ensure the generator is properly mounted and balanced.
3. Corrosion: Permanent magnet generators are susceptible to corrosion, especially when exposed to harsh weather conditions. The solution is to use corrosion-resistant materials and coatings.
4. Magnet demagnetization: Over time, the magnets in the generator may lose their magnetic properties. The solution is to use high-quality magnets and ensure proper maintenance and repair.
5. Voltage regulation: Permanent magnet generators may experience voltage fluctuations, which can damage connected devices. The solution is to use voltage regulators to stabilize the output voltage.
6. Electrical shorts: Electrical shorts can occur in the generator’s wiring, causing damage to the generator and connected devices. The solution is to ensure proper wiring and insulation.
7. Bearing failure: Bearings in the generator may fail over time, causing excessive noise and vibration. The solution is to ensure proper lubrication and maintenance of the bearings.
C. Safety Precautions
1. Proper grounding: Permanent magnet generators should be grounded properly to avoid electrical shocks and damage to the equipment.
2. Overcurrent protection: Overcurrent protection should be installed to prevent damage to the generator in the event of a short circuit or overload.
3. Regular maintenance: Regular maintenance of the generator is necessary to ensure its proper functioning and to prevent any accidents.
4. Proper ventilation: Permanent magnet generators should be placed in well-ventilated areas to prevent overheating and damage to the equipment.
5. Proper installation: Permanent magnet generators should be installed by professionals who have the necessary knowledge and experience to ensure safe installation.
6. Use of protective gear: Workers who work on or around permanent magnet generators should wear appropriate protective gear, including gloves, goggles, and earplugs.
7. Emergency shutdown: An emergency shutdown system should be installed to quickly shut down the generator in the event of an emergency.
8. Fire safety: Fire safety precautions should be taken, including the use of fire extinguishers, smoke detectors, and fire alarms.
9. Proper labeling: Permanent magnet generators should be properly labeled with warning signs and instructions for safe operation.
10. Proper training: Workers who operate or work on permanent magnet generators should be properly trained on safe operation and maintenance procedures.
VI. Conclusion— Future Developments and Trends
1. Increased Efficiency: One of the main trends in permanent magnet generators is increased efficiency. With advances in technology and materials, manufacturers are developing permanent magnet generators that can produce more power with less energy input. This means that they can generate more electricity while reducing their carbon footprint.
2. Higher Power Density: Another trend is the development of permanent magnet generators with higher power densities. This means that they can produce more power in a smaller package, which is particularly useful for applications where space is limited.
3. Improved Durability: Permanent magnet generators are already known for their durability, but manufacturers are working to improve this even further. This includes using more robust materials and designs that can withstand harsh environments and extreme temperatures.
4. Integration with Renewable Energy Sources: As the use of renewable energy sources such as wind and solar power continues to grow, there is a need for generators that can efficiently convert this energy into electricity. Permanent magnet generators are well-suited for this task, and manufacturers are developing models that are specifically designed to work with renewable energy sources.
5. Smart Grid Integration: Another trend is the integration of permanent magnet generators with smart grid technology. This allows for better monitoring and control of electricity production and consumption, which can help to improve efficiency and reduce costs.
Overall, the future of permanent magnet generators looks bright, with continued advancements in technology and materials leading to more efficient, durable, and versatile generators that can help to power the world’s growing energy needs.