I. Introduction
– The importance of wind energy and the need for efficient wind turbines
Wind energy is important because it is a clean and renewable source of energy that can help reduce greenhouse gas emissions and combat climate change. Wind turbines are machines that harness the power of the wind to generate electricity. The efficiency of wind turbines is important because it determines how much energy can be produced from a given amount of wind. More efficient wind turbines can generate more energy, which is important for increasing the amount of renewable energy in the grid and reducing reliance on fossil fuels. Additionally, efficient wind turbines can help reduce the cost of wind energy and make it more competitive with other forms of energy.
– The role of permanent magnet generators in wind turbine applications
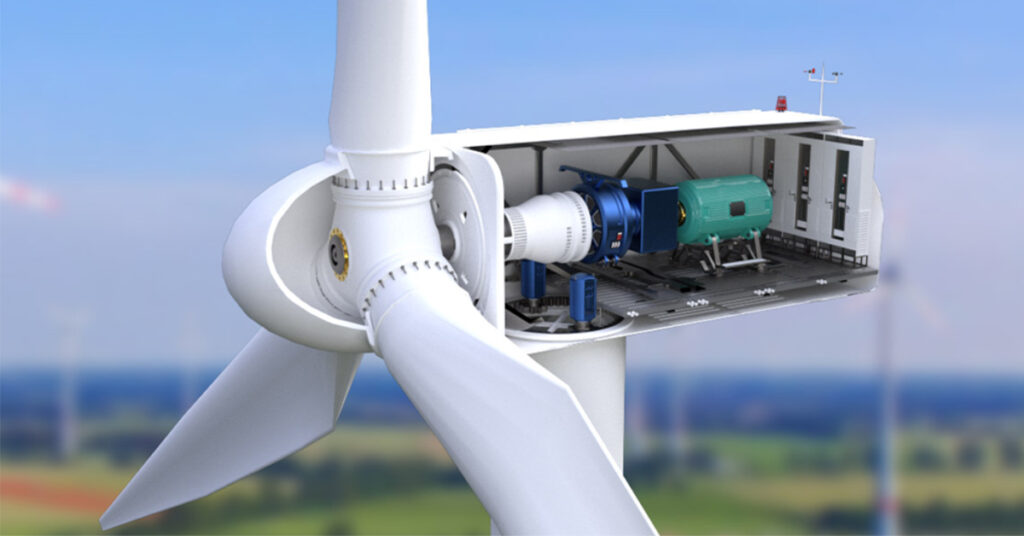
Permanent magnet generators (PMGs) are a crucial component in wind turbine applications. They are responsible for converting the rotational energy of the wind turbine blades into electrical energy that can be used by homes, businesses, and other electrical systems.
PMGs are typically located at the top of the wind turbine tower and are connected to the turbine blades through a gearbox. As the blades rotate, they turn the shaft of the generator, which in turn produces electrical energy through the interaction between the magnetic field of the permanent magnets and the stator windings.
One of the key benefits of using PMGs in wind turbines is their efficiency. PMGs have a higher power density than other types of generators, meaning they can produce more electrical energy for a given size and weight. Additionally, PMGs have fewer moving parts than traditional generators, reducing the risk of mechanical failure and increasing the overall reliability of the system.
Another advantage of PMGs is their ability to operate at variable speeds. Wind speed can vary widely depending on the location and time of day, and PMGs can adjust their output to match these changes. This allows wind turbine systems to operate more efficiently and produce more energy overall.
– Introduction of the design and fabrication of radial flux permanent magnet generator for wind turbine applications
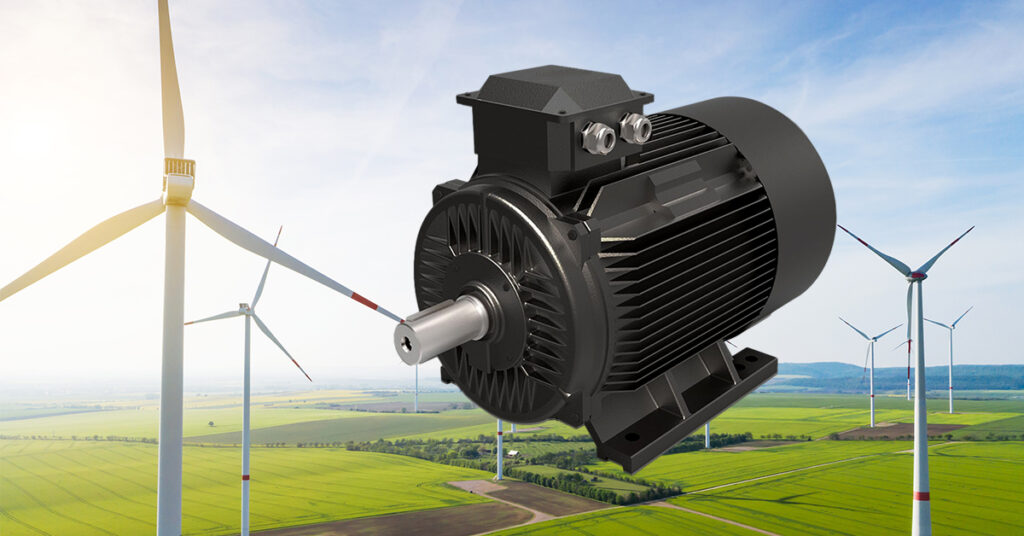
Wind energy is one of the most promising renewable energy sources, and its utilization has been growing steadily in recent years. To harness wind energy, wind turbines are used, which convert the kinetic energy of the wind into electrical energy. One of the critical components of wind turbines is the generator, which converts the mechanical energy from the rotor into electrical energy. Permanent magnet generators (PMGs) are widely used in wind turbine applications due to their high efficiency, low maintenance, and compact size.
In this paper, we present the design and fabrication of a radial flux PMG for wind turbine applications. The generator’s design is based on a radial flux topology, which has several advantages over other topologies, including high power density, low cogging torque, and reduced weight. The PMG consists of a stator and a rotor. The stator is composed of laminated steel sheets with slots for winding, and the winding is made of copper wire. The rotor is composed of permanent magnets arranged in a radial pattern, which generates a magnetic field that interacts with the stator winding.
The fabrication process includes the design of the stator and rotor, the selection of materials, and the manufacturing process. The stator and rotor are fabricated separately and assembled to form the PMG. The stator is made of laminated steel sheets, which are stacked and punched to form slots for winding. The winding is then inserted into the slots, and the stator is coated with an insulating material. The rotor is made of permanent magnets, which are arranged in a radial pattern and fixed to a central shaft. The shaft is supported by bearings, which allow it to rotate freely.
In conclusion, the PMG has several advantages over other topologies, including high power density, low cogging torque, and reduced weight. The fabrication process includes the selection of materials and the manufacturing process, which involves the fabrication of the stator and rotor separately and their subsequent assembly. The PMG’s performance can be improved by optimizing the design parameters and materials used.
II. Design considerations for radial flux permanent magnet generator
– Explanation of the radial flux topology and its advantages in wind turbine applications
A radial flux topology is a design approach used in the construction of electric generators in wind turbines. This topology is characterized by the placement of the stator and rotor in a radial configuration, with the stator surrounding the rotor. In this configuration, the magnetic flux flows radially between the rotor and stator, hence the name “radial flux.”
The advantages of radial flux topology in wind turbine applications include:
1. Higher power density: Due to the compact nature of the radial flux design, it allows for a higher power density than other designs. This means that the generator can produce more power in a smaller space, making it ideal for wind turbines, where space is often limited.
2. Improved efficiency: The radial flux topology allows for a more efficient transfer of energy from the rotor to the stator. This is because the magnetic flux path is shorter, and there is less resistance to the flow of energy.
3. Lower weight: The compact design of the radial flux topology means that it is lighter than other designs, making it easier to install and transport.
4. Reduced maintenance: The radial flux topology is less prone to wear and tear, as the magnetic flux flows radially, reducing the friction between the rotor and stator. This means that it requires less maintenance and has a longer lifespan.
Overall, the radial flux topology is an ideal design approach for wind turbine generators, as it offers higher power density, improved efficiency, lower weight, and reduced maintenance requirements.
– Design considerations when choosing the permanent magnet generators
1. Number of poles: The number of poles in a permanent magnet generator is an essential design consideration as it determines the generator’s speed and output voltage. The higher the number of poles, the lower the rotational speed required to produce the same output voltage. However, a higher number of poles also means a more massive and more expensive generator.
2. Magnet material: The choice of magnet material is another critical design consideration in permanent magnet generators. The most commonly used magnet materials are neodymium, samarium-cobalt, and ferrite. Neodymium magnets are the most powerful and efficient, but they are also the most expensive. Ferrite magnets are less expensive but have lower magnetic strength. Samarium-cobalt magnets are a balance between the two, with high magnetic strength and a moderate price.
3. Coil arrangement: The coil arrangement in a permanent magnet generator determines the output voltage and current. There are two types of coil arrangements: single-phase and three-phase. Single-phase generators are simpler and less expensive but produce less power than three-phase generators. Three-phase generators are more complex and expensive but produce higher power output.
4. Stator and rotor design: The stator and rotor design of a permanent magnet generator are crucial in determining the efficiency and power output of the generator. The stator is the stationary part of the generator, and the rotor is the rotating part. The stator and rotor design should be optimized to minimize losses due to eddy currents and hysteresis.
5. Cooling system: The cooling system is another critical design consideration in permanent magnet generators. The generator’s efficiency and lifespan depend on maintaining the magnets’ temperature within an acceptable range. The cooling system can be air-cooled or liquid-cooled, depending on the generator’s size and application.
6. Mechanical design: The mechanical design of a permanent magnet generator should be robust and durable to withstand mechanical stresses and vibrations. The generator’s mounting, bearings, and shafts should be designed to minimize friction and wear. The generator’s housing should be sealed to prevent dust and moisture from entering the generator.
III. Fabrication process for radial flux permanent magnet generator
The fabrication process for a radial flux permanent magnet generator involves several steps, including the selection of materials and manufacturing techniques. The following are the steps involved in the fabrication process of a radial flux permanent magnet generator:
1. Magnet Selection: The first step in the fabrication process is the selection of the permanent magnet material. The most commonly used materials for permanent magnets are neodymium, samarium-cobalt, and ferrite. The choice of the magnet material depends on the required magnetic field strength, temperature range, and cost.
2. Stator and Rotor Design: Once the magnet material is selected, the stator and rotor design is created. The stator and rotor design will determine the shape, size, and number of magnets and coils used in the generator.
3. Coil Winding: The next step is to wind the coils onto the stator. The coils are typically made of copper wire and are wound around the stator in a specific pattern to generate the required voltage and current.
4. Magnet Placement: The permanent magnets are then placed on the rotor in a specific pattern to create a magnetic field. The placement of magnets is critical to ensure maximum efficiency and power output.
5. Assembly: Once the stator and rotor are complete, they are assembled together. The assembly process involves aligning the stator and rotor correctly and securing them in place.
6. Testing: The final step is to test the generator to ensure that it is functioning correctly. The generator is tested for power output, efficiency, and durability.
Manufacturing techniques for radial flux permanent magnet generators include casting, forging, and machining. The manufacturing technique used depends on the size and complexity of the generator. Casting is often used for larger generators, while machining is used for smaller generators. Forging is used for high-strength applications where the generator needs to withstand high forces and temperatures.
–The challenges involved in manufacturing high-performance generator
1. Design: The design of a high-performance generator must be carefully planned and optimized to ensure maximum efficiency and performance. This requires a thorough understanding of the physics and engineering principles involved in generator design, as well as the specific requirements of the application.
2. Materials: High-performance generators require high-quality materials that can withstand the stresses and strains of operation at high speeds and temperatures. This includes materials for the rotor and stator, as well as the bearings and other components.
3. Manufacturing processes: The manufacturing processes used to produce high-performance generators must be precise and accurate, as even small variations can have a significant impact on performance. This requires specialized equipment and skilled technicians.
4. Testing and validation: High-performance generators must undergo rigorous testing and validation to ensure that they meet the required performance specifications. This includes testing under a range of operating conditions, as well as testing for durability and reliability.
5. Cost: Manufacturing a high-performance generator can be expensive, due to the high-quality materials, specialized equipment, and skilled labor required. This can make it difficult to produce these generators at a price point that is competitive with lower-performing models.
– Explanation of the testing and validation process to ensure generator performance meets design specifications
The testing and validation process is a critical step in ensuring that a generator’s performance meets the design specifications. This process involves a series of tests that are designed to evaluate the generator’s performance under various operating conditions and loads. The following are the steps involved in the testing and validation process:
1. Functionality testing: This involves testing the generator to ensure that all its components are functioning correctly. This includes testing the electrical and mechanical components, such as the stator, rotor, bearings, and cooling system.
2. Load testing: This involves subjecting the generator to various loads to evaluate its ability to perform under different conditions. The generator may be tested under full load, half load, and no load conditions.
3. Efficiency testing: This involves measuring the generator’s efficiency under different loads. The efficiency of the generator is an important factor as it determines how much fuel is required to produce a given amount of power.
4. Voltage regulation testing: This involves testing the generator’s ability to maintain a stable voltage output under different loads. Voltage regulation is critical as it ensures that the generator can provide consistent power output to the connected load.
5. Noise and vibration testing: This involves measuring the noise and vibration levels produced by the generator under different loads. This is important as excessive noise and vibration can cause damage to the generator and other equipment.
6. Environmental testing: This involves subjecting the generator to different environmental conditions, such as temperature, humidity, and altitude. This is important as the generator may be used in different environments, and it needs to be able to perform under these conditions.
Once the testing and validation process is complete, the data is analyzed to ensure that the generator meets the design specifications. Any issues identified during testing are addressed, and the generator is retested until it meets the required standards. Once the generator is deemed to be in compliance with the design specifications, it can be certified as ready for use.
IV. Performance evaluation of radial flux permanent magnet generator
1. Power output testing: This involves measuring the generator’s power output in terms of voltage and current. The power output can be measured using a digital multimeter or a power analyzer. The generator is connected to a load bank that is designed to simulate the real-world load that the generator will face.
2. Efficiency testing: This involves measuring the generator’s efficiency, which is the ratio of the electrical energy output to the fuel energy input. The efficiency can be measured using a fuel flow meter and a power analyzer. The generator is run at various loads and the fuel consumption and power output are measured to calculate the efficiency.
3. Durability testing: This involves subjecting the generator to various stress tests to evaluate its durability and reliability. The generator is subjected to extreme temperatures, vibrations, and other environmental conditions to simulate real-world operating conditions. The generator is also subjected to overload conditions to test its overload capacity.
4. Load testing: This involves measuring the generator’s ability to handle varying loads. The generator is connected to a load bank and subjected to varying loads to evaluate its performance under different load conditions.
5. Fuel consumption testing: This involves measuring the generator’s fuel consumption under different load conditions. The generator is run at various loads and the fuel consumption is measured to evaluate its fuel efficiency.
6. Noise testing: This involves measuring the generator’s noise level at different load conditions. The generator is placed in an acoustic chamber and the noise level is measured using a sound level meter. This helps to evaluate the generator’s noise performance and compliance with noise regulations.
– Comparison of the performance of radial flux permanent magnet generators to other generator topologies commonly used in wind turbine applications
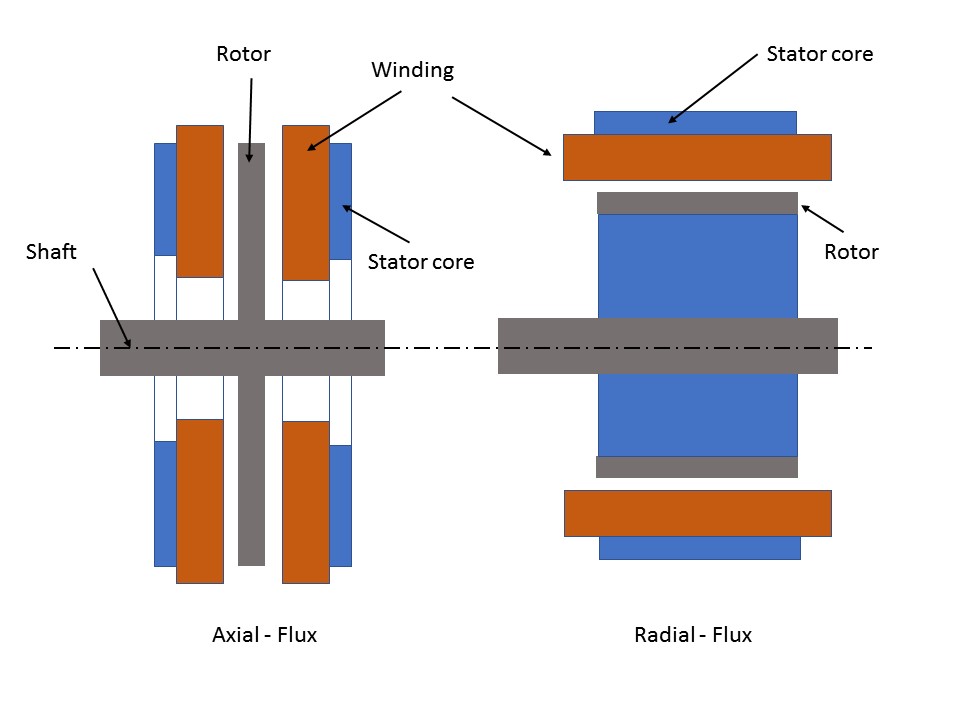
Radial flux permanent magnet generators (RFPMGs) are increasingly being used in wind turbine applications due to their high efficiency, compact size, and low maintenance requirements. However, there are other generator topologies that are commonly used in wind turbines, such as axial flux permanent magnet generators (AFPMGs) and doubly fed induction generators (DFIGs). In this article, we will compare the performance of RFPMGs to these other generator topologies in terms of efficiency, power density, and cost.
Efficiency
RFPMGs are known for their high efficiency, which is typically above 95%. This is because they have a shorter magnetic path length, which reduces the losses due to eddy currents and hysteresis. AFPMGs also have high efficiency, but their efficiency is slightly lower than that of RFPMGs due to their longer magnetic path length. DFIGs, on the other hand, have lower efficiency than both RFPMGs and AFPMGs due to the need for slip rings and brushes, which increase the losses.
Power density
RFPMGs have a higher power density than AFPMGs due to their compact size and the ability to use multiple rotor and stator segments. This allows for a larger active area and a higher power output per unit volume. DFIGs have a lower power density than both RFPMGs and AFPMGs due to their larger size and the need for additional components such as slip rings and brushes.
Cost
RFPMGs are generally more expensive than AFPMGs due to the higher cost of the materials used in their construction, such as neodymium magnets. However, the higher efficiency and power density of RFPMGs can result in lower overall system costs due to the reduced size and weight of the generator. DFIGs are generally the least expensive option, but their lower efficiency and power density can result in higher overall system costs due to the need for additional components such as power electronics and cooling systems.
Overall, RFPMGs offer the highest efficiency and power density, but at a higher cost than AFPMGs. DFIGs are the least expensive option but offer lower efficiency and power density. The choice of generator topology will depend on the specific requirements of the wind turbine application, such as power output, size, and cost constraints.
V. Conclusion
– The implications of radial flux permanent magnet generator design and fabrication on the future of wind energy
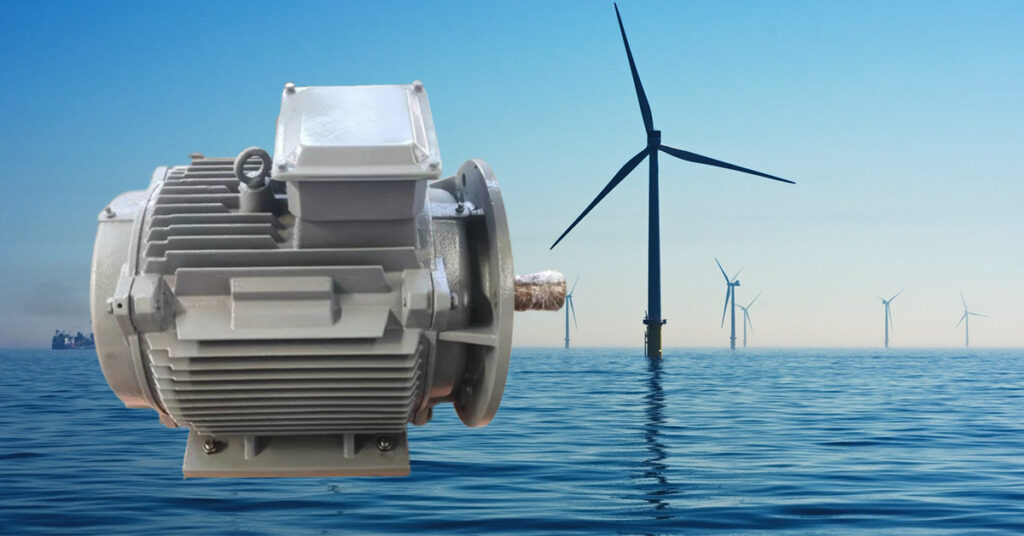
Radial flux permanent magnet generator design and fabrication have significant implications for the future of wind energy. These generators are more efficient, reliable, and durable than traditional generators used in wind turbines. They offer higher power density, lower weight, and reduced maintenance costs, making them an attractive option for wind energy projects.
One of the key advantages of radial flux permanent magnet generators is their ability to generate electricity at low wind speeds. This means that wind turbines equipped with these generators can start producing power at wind speeds as low as 3-4 meters per second, making them ideal for use in areas with low wind speeds. This can significantly increase the potential for wind energy production in regions that were previously considered unsuitable for wind turbines.
Another advantage of radial flux permanent magnet generators is their high efficiency. These generators can convert up to 96% of the kinetic energy from the wind into electrical energy, compared to traditional generators that can only convert around 60-70%. This means that wind turbines equipped with these generators can produce more electricity from the same amount of wind, reducing the number of turbines needed to generate the same amount of power.
Radial flux permanent magnet generators are also more durable and reliable than traditional generators. They have fewer moving parts, which means there are fewer components that can fail or wear out. This reduces maintenance costs and increases the lifespan of the generators, making them a more cost-effective option in the long run.
Overall, the use of radial flux permanent magnet generators in wind turbines has the potential to significantly increase the efficiency, reliability, and cost-effectiveness of wind energy generation. As the technology continues to develop and become more widely adopted, we can expect to see even greater improvements in the performance and affordability of wind energy.